What is Lean Six Sigma in Kentucky?
Contact Us
Why should you choose Six Sigma?
Six Sigma dates back to 1987 when Motorola introduced it. Following that, the creation of this quality control technique has been fascinating. Its development was sluggish at first, but it eventually gained popularity as a result of its positive results. As Jack Welch, then-CEO of General Electric, and Larry Bossidy, then-CEO of AlliedSignal, adopted Six Sigma in the mid-1990s, the technique’s early growth potential was recognized. Many companies all over the world have adopted and reaped the advantages of this approach since then.
Six Sigma was once considered a “management fad” on the way to being a quality management standard! Six Sigma, on the other hand, has rescued Fortune 500 companies and culminated in millions of dollars in real income. As a result, it has shown that it is more than just a management fad.
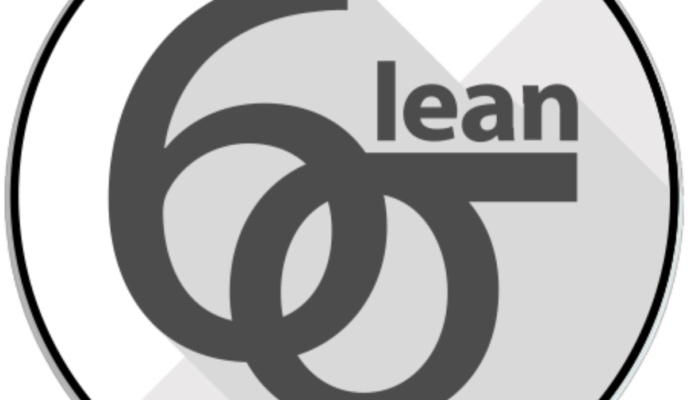
The Advantages of Using Six Sigma
When employed with accuracy and discipline, the Six Sigma approach has many operational advantages. It boosts consumer satisfaction and retention; all long-term companies aim to maintain their current clients. Clients can stick faithfully to your brand when you can sustain consumer satisfaction rather than moving to a different supplier or product offering. Are you worried about customers who are dissatisfied with the service offerings? Many companies may be unaware of this reality, and they may be targeting market growth without understanding their consumer satisfaction ratings.
When you use Lean Six Sigma Experts of Kentucky’s Six Sigma approach, you remove the risk of disgruntled consumers. We conduct a consumer dipstick test to help understand the fundamental qualities of your service or commodity, which is needed for customer satisfaction and good user experience improvement. We ensure that important products that can pique buyer curiosity and allow you to expand your client base are not overlooked when developing a business growth plan.
In today’s business environment, a combination of market expertise, efficiency, cutting-edge technology, and strict quality control is needed. Do you want your company to be recognized as a forerunner in its field? Is achieving a strategic advantage over your rivals one of your key market goals? Six Sigma methodologies are used to improve available capital efficiency.
Frequently Asked Questions
The world of today is on the brink of change. The only distinction, if any, is that the rate of transition accelerates with each passing year. The role of management in an enterprise is to create systems and value manufacturing and delivery systems for consumers and company owners; this is a continuous process. Competitors must change in order to attract consumers. Innovations alter the way goods and services are delivered to consumers. Customer tastes are changing at a breakneck rate. What appeals to you now may become a necessity tomorrow. The "transform imperative" is one concept shared by all organizations. Organizations that want to be transformational leaders must evolve or perish. Lean Six Sigma Experts of Kentucky are on board with the shift. We promote continual enhancement in methodology consistency and timeliness. Management must always be on the lookout for innovative approaches for their product and service offerings. Instead of a collection of services, operational reform becomes a way of life. Lean Six Sigma is both a system and a collection of techniques. Managers can utilize these as a resource when encouraging innovation in their respective fields. Black Belts and Master Black Belts serve in the administration and development departments of the organization. This indicates that Six Sigma is on the right track and is aiding organizations in achieving their targets. Performance is crucial when choosing the best Lean Six Sigma partner, as with selecting every other partner, provider, or supplier; it seems only appropriate to extend expertise to designing a few frequently asked questions when assessing prospective partners. Here are some commonly asked questions, along with some insight into the types of responses to be expected: Your Lean Six Sigma partner should at the very least have a Six Sigma delivery and teaching model in place, as well as an accomplished Master Black Belt on hand to support, train, and mentor on ventures. The Master Black Belt should have real-world experience and be familiar with the unique characteristics of your company, climate, and customers. During their preparation, candidates can create tools and adapt them to real-world scenarios. Project-based course management also necessitates the implementation of project result indicators, such that learners may translate their training interactions into real-world project results. This involves measuring dollars realized, cycle times, and timetable slippage, as well as “toll-gates”, to guarantee that tasks are completed on budget and with high quality. The Master Black Belt will also generate coaching assessments to consider and resolve personal and operational project issues. It is important to consider an organization's ability to implement a Lean Six Sigma strategy in order to create a difference. Your partner in excellence will sketch out exercises for a readiness assessment and lay the foundation for continuous deployment. This involves evaluating ongoing efforts that are in the works or are in the process of being expanded, as well as recognizing potential progress measures and possible programs. A planning assessment should provide an analysis of potential improvement areas identified in a void report, as well as a summary of consumer and market survey results. Both of these elements can aid in the identification of potential development risks, which can then be resolved. Six Sigma employs mathematical methods to analyze scenarios and evaluate outcomes. Six Sigma calculations are based on inferential statistics and probability hypotheses. However, Six Sigma is more than just numbers. It is a collection of approaches for defining what the consumer wants and aligning the organization and services, such as measuring systems, to satisfy those wants. Six Sigma decreases the number of surprises (variation) and increases objectivity in assessing results, especially in customer delivery execution. To be a Six Sigma specialist, you must have a strong desire to offer excellent customer service, be able to challenge the status quo daily and provide a basic understanding of statistics. Why Six Sigma?
How does Lean Six Sigma work?
How do you handle managing classes through their projects?
How can you incorporate your program with the work that our company is already doing?
Six Sigma is about statistics, do I need to learn statistics?
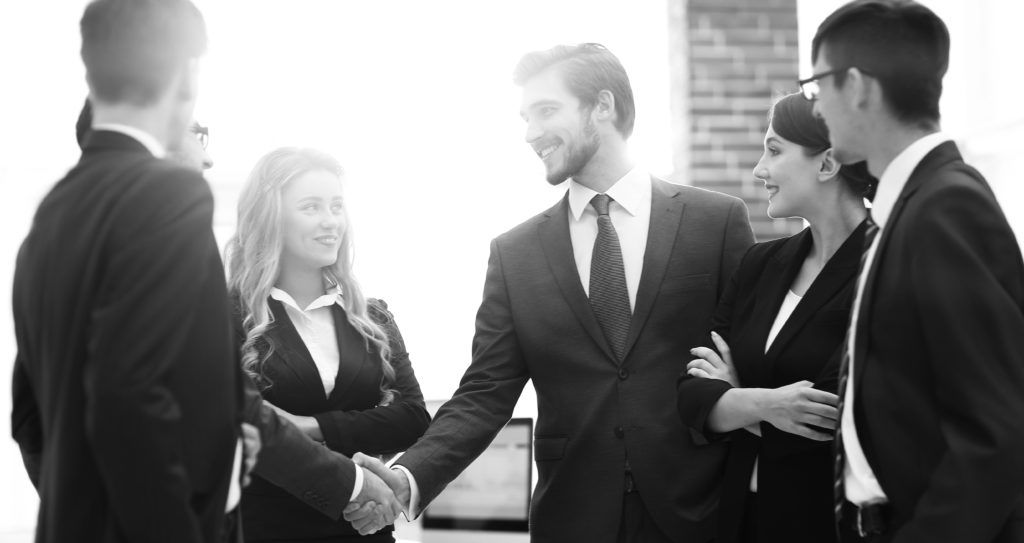
What is the difference between Six Sigma and Lean?
The Lean method is used to remove waste in a systematic manner (called Muda in Japanese). There are seven types of waste, according to Taiichi Ohno (TPS fame). To deliver value to consumers, it is critical to recognize and eliminate all of the waste.
To improve company operations and efficiency, both the Lean and Six Sigma methodologies are used. Lean is more about systems, maximizing movement, and improving performance. Six Sigma is concerned with increasing production, success, and efficiency.
There are so many areas or regions where we offer these services with most of them being cities.
However, if you need any of these services, you need to contact us. The list below comprises the areas where we offer these services.